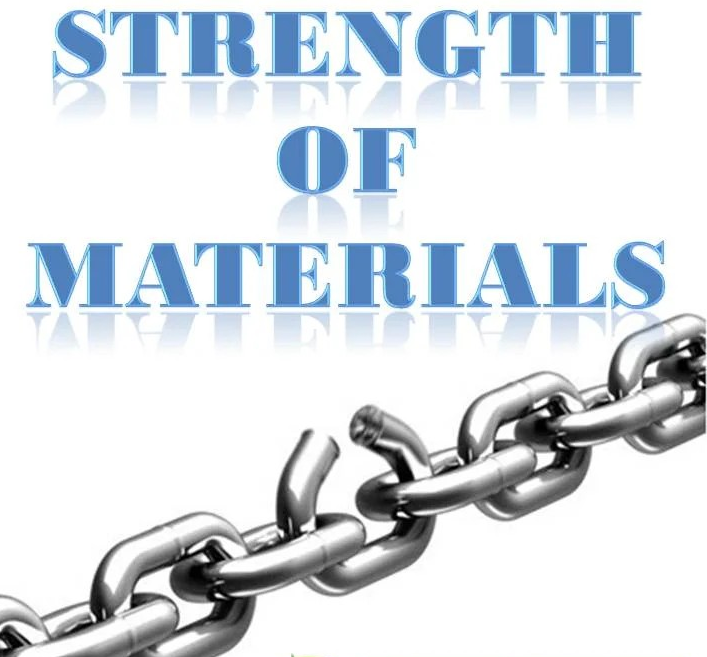
1. What is stress?
Answer:
Stress is the internal resistance offered by a material to counteract an external force acting on it. It is calculated as the force per unit area and is a measure of how much internal force is generated within a material. The unit of stress is Pascal (Pa) or N/m².
Formula:
Stress = Force (F) / Area (A)
There are different types of stresses: tensile, compressive, and shear stress, depending on the direction of the force.
2. Define strain.
Answer:
Strain is the measure of deformation or elongation of a material when stress is applied. It is a dimensionless quantity (no units) because it is the ratio of change in length to the original length.
Formula:
Strain = ΔL / L
where ΔL is the change in length, and L is the original length. Strain can also be of different types like tensile strain, compressive strain, and shear strain.
3. What is Hooke’s Law?
Answer:
Hooke’s Law describes the linear relationship between stress and strain in the elastic region of a material’s deformation. It states that within the elastic limit, the stress is directly proportional to strain.
Mathematical Form:
σ = E × ε
where:
– σ: stress
– ε: strain
– E: Young’s modulus or modulus of elasticity
This law is fundamental in calculating deformations and designing components within safe limits.
4. What is Young’s modulus?
Answer:
Young’s modulus, also known as the modulus of elasticity, is a material constant that defines the stiffness of a material. It is the ratio of tensile stress to tensile strain in the linear elastic region.
A higher value of Young’s modulus indicates a stiffer material.
Formula:
E = Stress / Strain = σ / ε
Example: Steel has a Young’s modulus of approximately 200 GPa, which means it is quite stiff compared to materials like rubber.
5. Differentiate between tensile and compressive stress.
Answer:
- Tensile Stress: Occurs when forces act to pull the material apart, increasing its length. Example: A rod being pulled at both ends.
- Compressive Stress: Occurs when forces act to push the material together, reducing its length. Example: A column loaded at the top.
Both are types of normal stresses and are calculated using the same basic formula:
Stress = Force / Area
However, tensile stress is considered positive and compressive stress negative in sign convention.
6. What is the elastic limit?
Answer:
The elastic limit is the maximum stress that a material can withstand without undergoing permanent deformation. When the applied stress exceeds this limit, the material will not return to its original shape after the load is removed, leading to plastic deformation. The elastic limit marks the end of the elastic region on the stress-strain curve.
7. Define plastic deformation.
Answer:
Plastic deformation refers to the permanent change in shape or size of a material after the applied stress exceeds the elastic limit. Unlike elastic deformation, plastic deformation does not reverse when the load is removed. It occurs due to the movement of dislocations within the material’s crystal structure.
8. What is Poisson’s ratio?
Answer:
Poisson’s ratio is the ratio of lateral strain to longitudinal strain in a material subjected to axial stress. When a material is stretched or compressed, it tends to contract or expand laterally. Poisson’s ratio quantifies this effect.
Formula:
ν = – (Lateral Strain) / (Longitudinal Strain)
The negative sign indicates that lateral strain and longitudinal strain have opposite signs (one contracts while the other elongates). Typical values of Poisson’s ratio for metals range from 0.25 to 0.35.
9. What are ductile materials?
Answer:
Ductile materials are those that can undergo significant plastic deformation before fracture. They can be stretched into wires or undergo bending without breaking. Ductility is an important property in materials used in construction and manufacturing, as it allows energy absorption and warning before failure.
Examples: Steel, copper, aluminum.
10. What are brittle materials?
Answer:
Brittle materials break suddenly without significant plastic deformation. They fracture with little warning and absorb less energy before failure. Brittle materials typically fail at stresses lower than their tensile strength due to crack propagation.
Examples: Glass, cast iron, ceramics.
11. What is shear stress?
Answer:
Shear stress is the component of stress that acts parallel or tangential to the surface of a material. It occurs when forces are applied in opposite directions but along parallel planes within the material.
Formula:
τ = F / A
where τ is shear stress, F is the applied force, and A is the area over which the force acts.
12. What is shear strain?
Answer:
Shear strain is the measure of the angular distortion produced in a material due to shear stress. It is defined as the change in angle (in radians) between two originally perpendicular lines in the material.
Formula:
γ = tan θ ≈ θ (for small angles)
where γ is shear strain and θ is the angular deformation in radians.
13. What is the modulus of rigidity?
Answer:
The modulus of rigidity, also known as the shear modulus (G), is the ratio of shear stress to shear strain in the elastic region.
Formula:
G = τ / γ
It measures the rigidity of a material against shear deformation. For example, steel has a shear modulus of approximately 80 GPa.
14. What is bulk modulus?
Answer:
Bulk modulus (K) measures a material’s resistance to uniform compression. It is the ratio of volumetric stress to volumetric strain.
Formula:
K = – (Pressure) / (Volumetric Strain) = -P / (ΔV / V)
where P is the applied pressure, V is the original volume, and ΔV is the change in volume. Materials with high bulk modulus, like steel, resist volume changes under pressure.
15. Define factor of safety.
Answer:
Factor of Safety (FoS) is the ratio of the maximum stress a material or structure can withstand (ultimate stress) to the allowable working stress.
Formula:
FoS = Ultimate Stress / Working Stress
It ensures designs operate safely below failure limits, accounting for uncertainties in load, material properties, and manufacturing defects. A typical FoS for mechanical components ranges from 1.5 to 3.
16. What is resilience?
Answer:
Resilience is the ability of a material to absorb energy when it is deformed elastically and release that energy upon unloading. It is the area under the elastic portion of the stress-strain curve.
Formula:
Resilience (U) = (1/2) × Stress × Strain = (σ²) / (2E)
where σ is stress and E is Young’s modulus.
17. What is proof resilience?
Answer:
Proof resilience is the maximum energy per unit volume that a material can absorb without undergoing permanent deformation. It corresponds to the area under the stress-strain curve up to the elastic limit.
This property is important in materials subject to sudden loads or shocks.
18. What is toughness?
Answer:
Toughness is the total energy a material can absorb before fracturing, representing both elastic and plastic deformation. It is the area under the entire stress-strain curve.
Materials with high toughness can withstand both high stress and strain, such as steel, while brittle materials have low toughness.
19. What is hardness?
Answer:
Hardness is the resistance of a material to deformation, particularly permanent indentation or scratching. It is measured by tests such as Brinell, Rockwell, and Vickers.
Higher hardness usually indicates better wear resistance.
20. What is creep?
Answer:
Creep is the slow, time-dependent deformation of a material under constant load or stress, usually at high temperatures. It can lead to failure over long periods even if the stress is below the yield strength.
Creep behavior is critical in components like turbine blades and boilers operating at elevated temperatures.
21. What is fatigue?
Answer:
Fatigue is the weakening or failure of a material caused by repeated cyclic loading, even if the maximum stress is below the material’s ultimate tensile strength. It occurs due to the initiation and growth of cracks over time, leading to sudden fracture.
22. What is endurance limit?
Answer:
Endurance limit is the maximum stress amplitude a material can withstand indefinitely without failing due to fatigue. Materials like steel have a defined endurance limit, while others like aluminum do not.
23. Define thermal stress.
Answer:
Thermal stress is the stress induced in a material when it undergoes a change in temperature but is constrained from expanding or contracting freely.
Formula:
σ = E × α × ΔT
where σ is thermal stress, E is Young’s modulus, α is the coefficient of thermal expansion, and ΔT is the temperature change.
24. What is a stress-strain curve?
Answer:
A stress-strain curve is a graphical representation showing the relationship between the stress applied to a material and the resulting strain. It illustrates the elastic region, yield point, plastic deformation, and fracture point, providing key mechanical properties.
25. What is strain energy?
Answer:
Strain energy is the energy stored in a material due to deformation under load. It is recoverable in the elastic region.
Formula:
U = (1/2) × Stress × Strain × Volume
This energy is released when the load is removed if the material is within the elastic limit.
26. What is bending moment?
Answer:
Bending moment at a section of a beam is the algebraic sum of moments about that section of all external forces acting to bend the beam. It causes bending stresses and deflections in beams.
27. What is shear force?
Answer:
Shear force at a section of a beam is the algebraic sum of all forces acting perpendicular to the beam axis on either side of the section. It causes shear stresses within the beam.
28. What is a moment of inertia?
Answer:
Moment of inertia (I) is a geometric property of a cross-section that indicates its resistance to bending. It depends on the shape and size of the cross-section.
Formula (for rectangular section):
I = (b × h³) / 12
where b = base width, h = height of the section.
29. What is the difference between simple bending and pure bending?
Answer:
- Simple Bending: Bending of a beam with varying bending moment along its length and presence of shear forces.
- Pure Bending: Bending of a beam section with constant bending moment and zero shear force, usually in the middle portion of a beam.
30. What is the neutral axis in bending?
Answer:
The neutral axis is an imaginary line in the cross-section of a bent beam where the fibers experience zero stress and zero strain during bending. Above the neutral axis, fibers are in compression; below, they are in tension.
31. What is the difference between ductile and brittle fracture?
Answer:
- Ductile fracture: Occurs with significant plastic deformation and energy absorption before failure. The fracture surface appears rough and fibrous.
- Brittle fracture: Occurs suddenly with little or no plastic deformation and low energy absorption. The fracture surface appears smooth and shiny.
32. What is the significance of the yield point in a material?
Answer:
The yield point is the stress level at which a material begins to deform plastically. Beyond this point, permanent deformation occurs even if the load is removed. It marks the transition from elastic to plastic behavior.
33. What is the difference between elastic deformation and plastic deformation?
Answer:
- Elastic deformation: Temporary deformation that disappears when the load is removed.
- Plastic deformation: Permanent deformation that remains after the load is removed.
34. Explain the term ‘modulus of elasticity’.
Answer:
Modulus of elasticity (Young’s modulus) is a measure of a material’s stiffness, defined as the ratio of stress to strain within the elastic limit.
Formula:
E = σ / ε
35. What is the difference between tensile strength and yield strength?
Answer:
- Tensile strength: The maximum stress a material can withstand while being stretched before breaking.
- Yield strength: The stress at which a material begins to deform plastically.
36. What is the difference between stress and strain?
Answer:
- Stress: Force per unit area within materials (σ = F/A).
- Strain: Measure of deformation representing the displacement between particles (ε = ΔL/L).
37. What is the significance of the area under the stress-strain curve?
Answer:
The area under the stress-strain curve represents the energy absorbed by the material per unit volume until failure. It indicates the toughness of the material.
38. What is the difference between isotropic and anisotropic materials?
Answer:
- Isotropic materials: Have identical mechanical properties in all directions.
- Anisotropic materials: Have direction-dependent properties.
39. What is meant by strain hardening?
Answer:
Strain hardening (or work hardening) is the increase in material strength and hardness due to plastic deformation, caused by dislocation movements obstructing further deformation.
40. What is torsion?
Answer:
Torsion is the twisting of an object due to an applied torque, resulting in shear stress over the cross section of the object, such as in shafts transmitting power.
41. What is the torsion formula?
Answer:
The torsion formula relates the applied torque (T), the shear stress (τ), the radius (r), and the polar moment of inertia (J) of a shaft:
Formula:
τ = (T × r) / J
where:
– τ = shear stress at a distance r from the center
– T = applied torque
– r = radial distance from the center
– J = polar moment of inertia of the cross section.
42. What is the polar moment of inertia?
Answer:
The polar moment of inertia (J) is a measure of an object’s ability to resist torsion. It depends on the geometry of the cross section.
Formula for circular shaft:
J = (π × d⁴) / 32
where d is the diameter of the shaft.
43. What is the difference between bending stress and shear stress?
Answer:
- Bending stress: Stress induced in a beam when subjected to bending moments; acts perpendicular to the cross section.
- Shear stress: Stress induced due to forces acting parallel to the cross section.
44. What is the maximum bending stress formula?
Answer:
Maximum bending stress in a beam section is given by:
Formula:
σ = (M × c) / I
where:
– σ = bending stress
– M = bending moment
– c = distance from neutral axis to outermost fiber
– I = moment of inertia of the section.
45. What is the relationship between Young’s modulus, shear modulus, and bulk modulus?
Answer:
The three moduli are related through Poisson’s ratio (ν) by the formula:
Formula:
E = 2G(1 + ν) = 3K(1 – 2ν)
where:
– E = Young’s modulus
– G = shear modulus
– K = bulk modulus
– ν = Poisson’s ratio.
46. What is strain energy density?
Answer:
Strain energy density is the strain energy stored per unit volume of the material.
Formula:
u = U / V = (1/2) × σ × ε
where:
– u = strain energy density
– U = total strain energy
– V = volume of material
– σ = stress
– ε = strain.
47. What is a neutral axis in torsion?
Answer:
In torsion, the neutral axis is the axis passing through the center of the shaft where shear stress is zero. The maximum shear stress occurs at the outer surface.
48. What is the importance of the moment of resistance?
Answer:
Moment of resistance is the internal moment developed by a beam’s cross section to resist external bending moments. It determines the beam’s load-carrying capacity.
49. What is the difference between direct stress and bending stress?
Answer:
- Direct stress: Stress caused by axial loads acting perpendicular to the cross section.
- Bending stress: Stress caused by bending moments producing tension and compression across the cross section.
50. What is the significance of the radius of gyration?
Answer:
The radius of gyration (k) is a measure of the distribution of cross-sectional area about an axis, defined as:
Formula:
k = √(I / A)
where I is the moment of inertia and A is the cross-sectional area.
It is important in buckling analysis of columns.
51. What is the difference between statically determinate and indeterminate structures?
Answer:
- Statically determinate: Structures where internal forces can be found using only equilibrium equations.
- Statically indeterminate: Structures requiring compatibility conditions in addition to equilibrium to solve for internal forces.
52. What is a strain gauge?
Answer:
A strain gauge is a sensor used to measure strain on an object by converting deformation into an electrical signal proportional to the strain.
53. What is the difference between ductility and malleability?
Answer:
- Ductility: Ability of a material to deform plastically under tensile stress (can be stretched into wires).
- Malleability: Ability of a material to deform plastically under compressive stress (can be hammered or rolled into sheets).
54. What is the significance of the Mohr’s circle in stress analysis?
Answer:
Mohr’s circle is a graphical method to determine principal stresses, maximum shear stresses, and stresses on inclined planes from known normal and shear stresses.
55. What is a principal stress?
Answer:
Principal stresses are the maximum and minimum normal stresses at a point, acting on mutually perpendicular planes where shear stress is zero.
56. What is the difference between average shear stress and maximum shear stress?
Answer:
- Average shear stress: Total shear force divided by the entire cross-sectional area.
- Maximum shear stress: Maximum value of shear stress occurring at a particular point, often at the neutral axis or surface depending on geometry.
57. What is the significance of the shear center?
Answer:
Shear center is the point on a cross-section through which the applied shear force causes bending without twisting the section.
58. What is the difference between bending moment diagram and shear force diagram?
Answer:
- Bending moment diagram: Graph showing variation of bending moment along the length of the beam.
- Shear force diagram: Graph showing variation of shear force along the length of the beam.
59. What is the effect of stress concentration?
Answer:
Stress concentration refers to localized increase in stress around discontinuities like holes, notches, or sudden changes in cross-section, which can lead to premature failure.
60. What is the factor of safety?
Answer:
Factor of safety (FoS) is the ratio of the maximum stress a material can withstand to the allowable working stress:
Formula:
FoS = Ultimate stress / Working stress
It ensures safety against unexpected loads or material defects.
61. What is creep in materials?
Answer:
Creep is the slow, time-dependent deformation of a material under constant stress at high temperature.
62. What are the three stages of creep?
Answer:
The three stages are:
1. Primary (decreasing creep rate)
2. Secondary (steady-state creep)
3. Tertiary (accelerating creep leading to failure)
63. What is fatigue failure?
Answer:
Fatigue failure occurs due to repeated cyclic loading causing crack initiation and growth, resulting in failure below the material’s ultimate tensile strength.
64. What is endurance limit?
Answer:
Endurance limit is the maximum stress amplitude a material can withstand indefinitely without fatigue failure.
65. What is the difference between axial load and eccentric load?
Answer:
Axial load acts along the centroidal axis, while eccentric load acts away from the centroid causing bending in addition to axial stress.
66. Define the term “buckling.”
Answer:
Buckling is sudden lateral deflection of a slender member subjected to compressive axial load beyond its critical load.
67. What is Euler’s critical load formula for buckling?
Answer:
\( P_{cr} = \frac{\pi^2 E I}{(K L)^2} \)
where Pcr = critical load, E = Young’s modulus, I = moment of inertia, L = length, K = effective length factor.
68. What is the slenderness ratio?
Answer:
Slenderness ratio is the ratio of effective length to radius of gyration:
\( \lambda = \frac{L}{k} \)
69. What is the difference between elastic and plastic buckling?
Answer:
Elastic buckling occurs when the material remains elastic during buckling; plastic buckling happens when the material yields before buckling.
70. What are columns and struts?
Answer:
Columns are vertical compressive members that carry axial loads. Struts are structural members subjected to compression but can be inclined.
71. What is shear force in beams?
Answer:
Shear force is the internal force in a beam acting perpendicular to its longitudinal axis caused by external loads.
72. What is the relation between shear force and bending moment?
Answer:
The derivative of bending moment with respect to length equals the shear force:
\( \frac{dM}{dx} = V \)
73. What is the significance of the neutral axis in bending?
Answer:
Neutral axis is the line within the cross section of a beam where the fibers experience zero stress during bending.
74. What is the moment of inertia?
Answer:
Moment of inertia is a geometric property of a cross section representing its resistance to bending or deflection.
75. What is the formula for the moment of inertia of a rectangular section?
Answer:
\( I = \frac{b h^3}{12} \)
where b = base width, h = height of the rectangle.
76. What is the difference between a beam and a shaft?
Answer:
Beams primarily resist bending loads; shafts primarily transmit torque causing torsion.
77. What is the difference between a statically determinate and statically indeterminate beam?
Answer:
Statically determinate beams can be analyzed with equilibrium equations alone; indeterminate beams require compatibility equations.
78. What is the significance of deflection in beams?
Answer:
Deflection is the displacement of a beam under load. Excessive deflection can lead to structural failure or serviceability issues.
79. What is a cantilever beam?
Answer:
A beam fixed at one end and free at the other, subjected to loads causing bending and shear.
80. What is the difference between a simply supported beam and a cantilever beam?
Answer:
Simply supported beams rest on supports at both ends and can rotate freely; cantilever beams are fixed at one end and free at the other.
81. What is the significance of the radius of curvature in bending?
Answer:
Radius of curvature is the radius of the curved beam axis after bending; it relates to the bending strain in the material.
82. What is the difference between the elastic curve and deflection curve?
Answer:
Elastic curve is the shape of the bent beam under load; deflection curve refers to the vertical displacement along the beam length.
83. What is the maximum shear stress in a circular shaft under torsion?
Answer:
Maximum shear stress occurs at the outer surface:
\( \tau_{max} = \frac{T c}{J} \)
where T = torque, c = outer radius, J = polar moment of inertia.
84. What is the difference between thin and thick cylinders?
Answer:
Thin cylinders have wall thickness less than 1/10th of diameter and experience uniform hoop stress; thick cylinders require more complex analysis with varying stress through thickness.
85. What is hoop stress?
Answer:
Hoop stress is the circumferential stress in a cylindrical vessel subjected to internal pressure.
86. What is longitudinal stress in pressure vessels?
Answer:
Longitudinal stress acts along the length of the vessel due to internal pressure.
87. What is the principal difference between axial and bending stresses?
Answer:
Axial stresses act uniformly over the cross section; bending stresses vary linearly from the neutral axis.
88. What is a composite beam?
Answer:
A beam made of two or more materials joined together to take advantage of their combined properties.
89. What is the modular ratio?
Answer:
Modular ratio (n) is the ratio of Young’s moduli of two materials in a composite section:
\( n = \frac{E_1}{E_2} \)
90. What is the significance of the transformed section in composite beams?
Answer:
Transformed section method converts composite beam into an equivalent section of one material to analyze stresses and strains.
91. What is thermal stress?
Answer:
Stress induced in a material due to temperature changes causing expansion or contraction.
92. What is the formula for thermal stress?
Answer:
\( \sigma = E \alpha \Delta T \)
where E = Young’s modulus, α = coefficient of thermal expansion, ΔT = temperature change.
93. What is the difference between static and dynamic loading?
Answer:
Static loading is applied slowly and remains constant; dynamic loading varies with time, such as impact or cyclic loading.
94. What is the significance of impact loading?
Answer:
Impact loading applies sudden force causing high stresses and possible failure beyond static limits.
95. What is a neutral axis in bending?
Answer:
Neutral axis is the line in the cross section where the bending stress is zero.
96. What is the difference between moment of inertia and radius of gyration?
Answer:
Moment of inertia (I) measures resistance to bending; radius of gyration (k) relates I to cross-sectional area (A) as \( k = \sqrt{I/A} \).
97. What is the importance of stress-strain curve?
Answer:
It shows material behavior under load, indicating elastic limit, yield point, ultimate strength, and failure point.
98. What is meant by the term “elastic limit”?
Answer:
Maximum stress that a material can withstand without permanent deformation.
99. What is the difference between proof stress and yield stress?
Answer:
Proof stress is the stress at a specified small permanent
100. What is the difference between proof stress and yield stress?
Answer:
Yield stress is the stress at which a material begins to deform plastically and permanent deformation occurs. It is often determined by a noticeable deviation from the linear portion of the stress-strain curve.
Proof stress, also called offset yield stress, is the stress corresponding to a specified small amount of permanent strain (commonly 0.2%). It is used when a clear yield point is not observed. Proof stress is determined by drawing a line parallel to the elastic portion of the stress-strain curve offset by 0.2% strain and finding the intersection with the curve.